How to reduce the blockage of concrete pump
Before the concrete pump pumps the concrete, clean water should be used to lubricate the pipeline, and the mortar is sent first, and then the concrete is sent to prevent blockage. When starting to pump, the concrete pump should be running at a slow and uniform speed, and then gradually accelerate. At the same time, the pressure of the concrete pump and the working conditions of each system should be observed. After each system is working normally, the pump can be pumped at normal speed. The concrete pumping work should be carried out as continuously as possible. The piston of the concrete cylinder should be kept running with a large stroke in order to perform the concrete pump. It can make the concrete cylinder wear evenly in the length direction. If the concrete pump has excessive pressure and is unstable, the oil temperature rises very high. When the conveying pipe is obviously vibrated and pumping is difficult, the pumping should not be forced, and the cause should be found out immediately and eliminated. You can first use a mallet to hit the bend of the conveying pipe. Conical pipes and other parts, and slow pumping or reverse pumping to prevent blockage.
In the hot summer, wet grass bags should be used to cover the pipes to prevent the concrete from falling too fast and causing pipe blockage during the pumping process.
The concrete pump hopper should be equipped with a screen, and a special person should be assigned to monitor the feed, and timely pick up large rocks and debris in time, especially rubble and long stones, etc., to avoid the entry of excessively large aggregates or foreign objects. Blocked.
When pumping, the concrete stock in the hopper should not be lower than the position of the mixing shaft to avoid air entering the pump pipe and causing pipe vibration.
After the pumping is completed, the hopper and the conveying pipeline system must be cleaned carefully. If the residual concrete in the concrete cylinder is not cleaned, it will solidify on the cylinder wall. When the piston runs again, the piston sealing surface will directly bear the impact of the solidified concrete on the cylinder wall, causing the pushing piston to partially peel off. This kind of damage is different from the normal wear and tear of the piston seal. The sealing surface cannot compensate itself under the action of pressure, resulting in slurry leakage or suction, causing pumping weakness, blockage, etc.
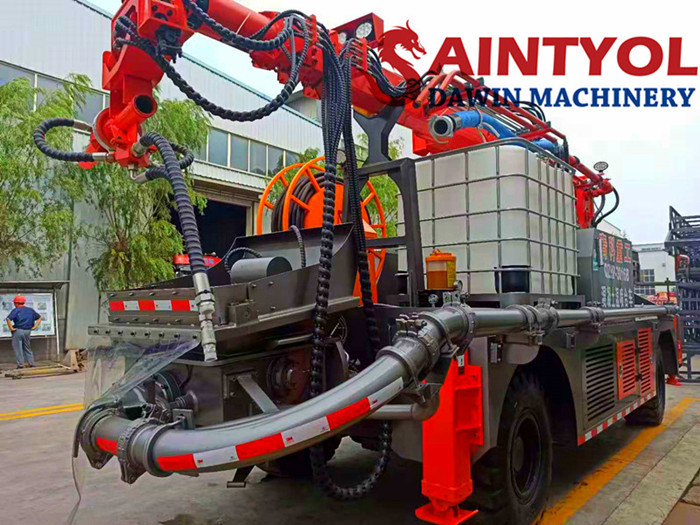