Thirteen questions about concrete aggregate, do you know?
(1) What matters should be paid attention to when entering coarse and fine aggregates?
Coarse aggregate should mainly control its particle size, gradation, grain shape, stone powder content, and mud content. Each vehicle shall undergo a macro inspection, and shall not be unloaded if it is unqualified; in addition, various indicators shall be inspected in batches in accordance with the requirements of the regulations. Fine aggregate should be controlled fineness modulus, mud content and mud content. Each vehicle shall undergo a macro inspection, and the unqualified vehicle shall not be unloaded; it shall also be inspected in batches according to the specifications.
(2) Why should the coarse aggregate particle size be controlled within 5-25mm?
The particle size of the coarse aggregate is restricted by the diameter of the concrete pumping pipeline and the pumping height. Generally, the large particle size that can be pumped decreases as the pumping height increases. For example, when the pumping height is less than 50m, the ratio of the large particle size of the coarse aggregate to the delivery diameter is ≤1:3; when the pumping height is 100m, the ratio will be reduced to 1:5, otherwise the pipe will be easily blocked.
(3) Why should the content of coarse aggregate needles and flakes be controlled for pumping concrete?
When its content is high, the flexural strength of the needle-shaped coarse aggregate is relatively low, and the bonding strength between the coarse aggregates decreases, which causes the strength of the concrete to decrease. For ready-mixed concrete, the high content of needles and flakes will make the coarse aggregates poorly shaped, which will reduce the fluidity of the concrete. At the same time, the needles and flakes are easy to block at the pipeline, causing the pump to block, or even burst pipes. . Therefore, the content of needles ≤10% is required for pumped concrete, and the requirement for high-strength concrete is even higher.
(4) What kind of sand does the ready-mixed concrete need?
Ready-mixed concrete needs to use medium sand. In addition to the standard requirements for sand gradation, mud content and mud content, it is also important to note that the sand passing through the 0.315mm sieve is not less than 15%. This has a great influence on the pumpability of concrete. If the value is too low, it will easily block the pump and make the concrete have poor water retention and bleeding.
(5) What are the effects of fine sand?
If the sand is too fine, the water demand of the concrete will increase. Moreover, the pumpability and plasticity retention of the concrete prepared with fine sand are extremely poor, the concrete strength will decrease, and the concrete will be easy to crack.
(6) What should I do if there is only fine sand?
If there is a problem with the sand source, fine sand and part of the machine-made sand can be used to prepare pumping concrete. For example, fine sand with a fineness modulus of less than 2.0 can be mixed with machine-made sand with a fineness modulus of 3.0-3.2, with a ratio of about 6:4. Observe its fluidity and pumpability, and determine the ratio through experiments.
(7) What are the consequences of the sand content conference?
The sand content is large, the concrete water demand is large, the plasticity is poor, the shrinkage is increased, the concrete strength is reduced, the structure is easy to crack, and the structure is easy to crack. Therefore, the sand content should be controlled ≤3% (C30-C50). The mud volume is more demanding.
(8) How will mud in sand and gravel affect concrete?
In addition to the same impact as mud in sand and gravel, it can also seriously affect the strength of concrete. For example, mud blocks will weaken the concrete cross-section; when the ground is poured, the mud blocks will float up, and will form pits and other defects on the surface after shrinking.
(9) Why should stones with a smaller particle size be used when preparing high-strength concrete?
As the particle size of the coarse aggregate increases, its bond with the cement paste is weakened, which increases the discontinuity of the internal structure of the concrete material, resulting in a decrease in the strength of the concrete.
(9) Coarse aggregate plays a constraining effect on cement shrinkage in concrete.
Because the elastic modulus of coarse aggregate and cement paste is different, tensile stress is generated inside the concrete. This internal stress increases with the increase of the coarse aggregate particle size, and will cause the concrete strength to decrease.
With the increase of the coarse aggregate particle size, the directional arrangement of Ca(OH)2 crystals in the transition zone of the coarse aggregate interface increases, and the interface structure is weakened, thereby reducing the strength of concrete. The test shows that the width of the interface cracks around the 15-25mm coarse aggregate in the concrete is about 0.1mm, and the crack length is 2/3 of the particle size circumference. There are more interface cracks connected with the cracks in the surrounding cement slurry: and 5 In the -10mm coarse aggregate concrete, the width of the interface crack is relatively uniform, only 0.03mm, and the crack length is only 1/6 of the perimeter of the particle size.
For coarse aggregates of different particle sizes, the accumulation of water sacs formed at the lower part of the particle size after concrete hardening is also different. The lower water sacs of large-size coarse aggregates are larger and more numerous. After the water in the water sacs evaporate, the lower interface is formed The interface seam must be wider than the small particle size, and the interface strength will be lower.
(10) Why is the strength of pebble concrete lower than that of gravel concrete by 3-4 MPa in the same proportion of concrete?
The surface of coarse aggregate is rough, which can be attributed to the interface strength between cement slurry and aggregate. According to the author’s many years of experimentation, on the one hand, the concrete prepared by pebble contains more weathered stones, its crushing index is lower than that of crushed stones, and the surface is smooth, and the interface strength is low. Therefore, the strength of concrete prepared by it will be higher than that of crushed stones of the same proportion. Concrete is 3-4 MPa lower.
(11) Why do we need to measure the moisture content of sand and gravel in every shift?
The amount of sand and gravel in the ready-mixed concrete is about 800-1100kg/m3, and every 1% of its water content will bring about 8-11kg of water in the concrete.
In particular, sand is usually collected from the river, and the moisture content varies greatly. If the moisture content is not frequently tested and the mixing water consumption is adjusted in time, it will cause great fluctuations in the slump, pumpability, and strength of the concrete.
(12) What is alkali aggregate reaction?
The alkali in the concrete chemically reacts with the aggregate chemical component of active silica, and the alkali-silicic acid gel is formed and swells after absorbing water. The expansion stress causes the concrete to crack. This process is called the alkali-aggregate reaction.
(13) How to prevent alkali aggregate reaction?
If the local coarse aggregate contains active silica, the alkali content of the concrete admixture must be strictly limited. For example, the "Specification for Concrete Structure Design" (GB50010) stipulates that when alkali active aggregate is used, the total alkali content of various materials in concrete is less than or equal to 3% of the concrete mass.
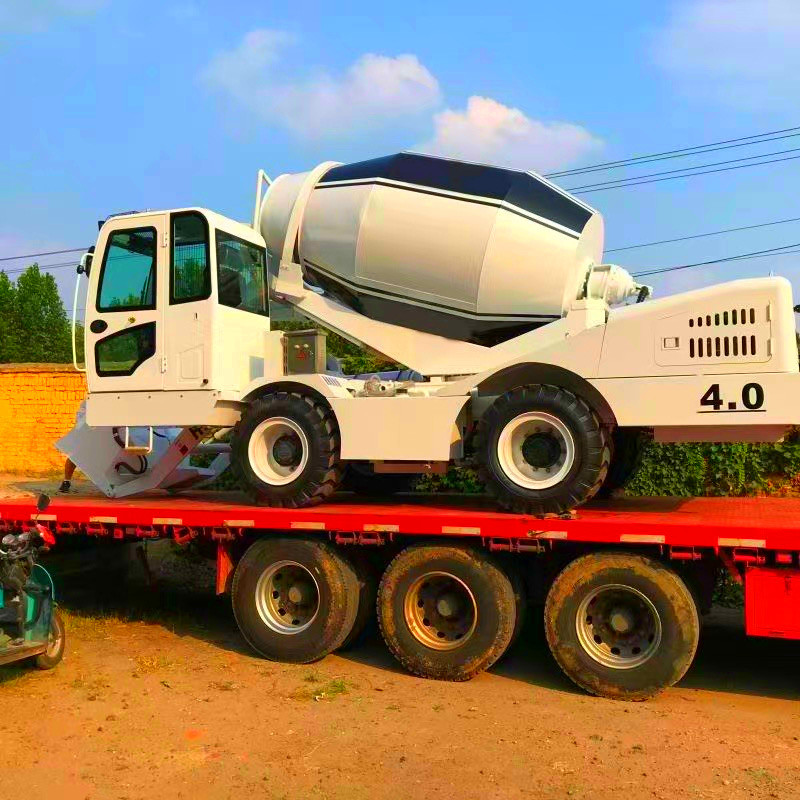