Tell you 8 ways to prevent concrete pipe plugging
1. Control workability and slump of concrete
The pumped concrete shall be designed in strict accordance with the regulations, the slump shall be strictly controlled, and the following principles shall be followed. (1) The ratio of the maximum particle size of coarse aggregate to the diameter of the conveying pipe should be: when the pumping height is below 50 m, it is not suitable for gravel
It should be greater than 1:3, and should not be greater than 1:2.5 for pebbles; when the pumping height is 50-100 m, the ratio should be 1:3-1:4;
When the height is above 100 m, the ratio should be 1:4~1:5. Coarse aggregate should be continuously graded, and the content of needle-like particles should not be
(1) The water-cement ratio of the pumped concrete should be 0.4-0.6.
(2) The sand content of the pumped concrete should be 38% to 45%. The fine aggregate should be medium sand, and the amount of sand passing through the 0.315 mm sieve should not be less than 15%.
2. Reasonably arrange the pipeline connection
Incorrect connection of pipes can easily lead to blocked pipes, and the following principles should be followed when connecting pipes.
(1) When designing and installing pipelines, avoid 90° and S-shaped bends as much as possible to reduce the resistance of pumping concrete, thereby reducing the possibility of pipe plugging.
(2) The taper pipe at the outlet of the pump is not allowed to directly connect to the elbow, at least it should be connected to a 5 m straight pipe before connecting to the elbow.
(3) For vertically downward pipelines, an anti-segregation device should be installed at the outlet to prevent pipe blockage.
(4) When pumping at high levels, the length of the horizontal pipeline should generally not be less than 15% of the length of the vertical pipeline, and a pipeline stop valve should be connected to the horizontal pipeline. When the shutdown time exceeds 5 minutes, the shut-off valve should be closed to prevent the concrete from backflowing and causing pipe blockage. For the 90° elbow when turning from horizontal to vertical, the radius of the elbow should be greater than 500 mm.
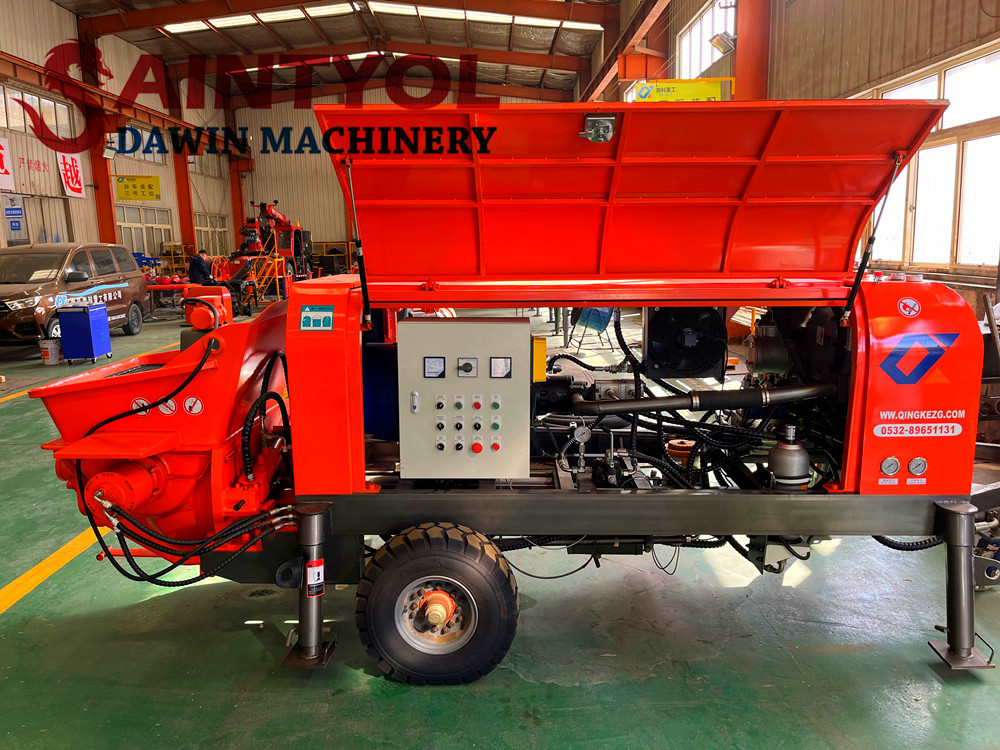
3. Check the sealing condition of the pipeline
Leakage caused by poor sealing of the pipeline will affect the pouring quality of the concrete on the one hand, and on the other hand will lead to a decrease in the slump of the concrete and a loss of pumping pressure, resulting in pipe plugging. The joints of the delivery pipeline are not tightly sealed, the pipe clamp is loose or the sealing ring is damaged, resulting in slurry leakage. At this time, the pipe clamp should be tightened or the sealing ring should be replaced. The piston is worn and should be replaced in time, otherwise the pipe will be blocked due to slurry leakage and pressure loss, and the wear of the piston and delivery cylinder will also be aggravated.
4. Lubricate the pipe wall
Before pumping concrete, the pipeline should be lubricated with clean water, and the mortar should be delivered first, followed by the concrete to prevent the pipeline from being blocked. After wetting the pipe with water before the pump, loosen the pipe joint from the lowest point of the pipe and drain all the remaining water, or put a sponge ball after pumping water and before pumping mortar to separate the mortar from the water. When cleaning the pipeline after pumping the concrete, a sponge ball should also be put in to separate the water from the concrete, otherwise it will easily cause pipe blockage. After pumping concrete, the hopper and pipeline system must be carefully cleaned. If the residual concrete in the cylinder is not cleaned, the concrete is easy to solidify on the cylinder wall. When the piston runs again, the sealing surface of the piston will directly bear the impact of the solidified concrete on the cylinder wall, resulting in partial peeling of the push piston. This kind of damage is different from the normal wear and tear of the piston seal. The sealing surface cannot self-compensate under the action of pressure, resulting in slurry leakage or air suction, resulting in weak pumping and pipe blockage.
5. Strictly control the amount of remaining material
When pumping concrete, the operator must observe the remaining material in the hopper at any time. The remaining material should not be lower than the stirring shaft. If the remaining material is too small, it is easy to inhale air and cause pipe blockage; and a filter screen should be installed on the concrete pump hopper, and Designate a special person to monitor the feeding status to prevent aggregates or foreign matter with too large diameter from entering the pump pipe, which will eventually cause blockage.
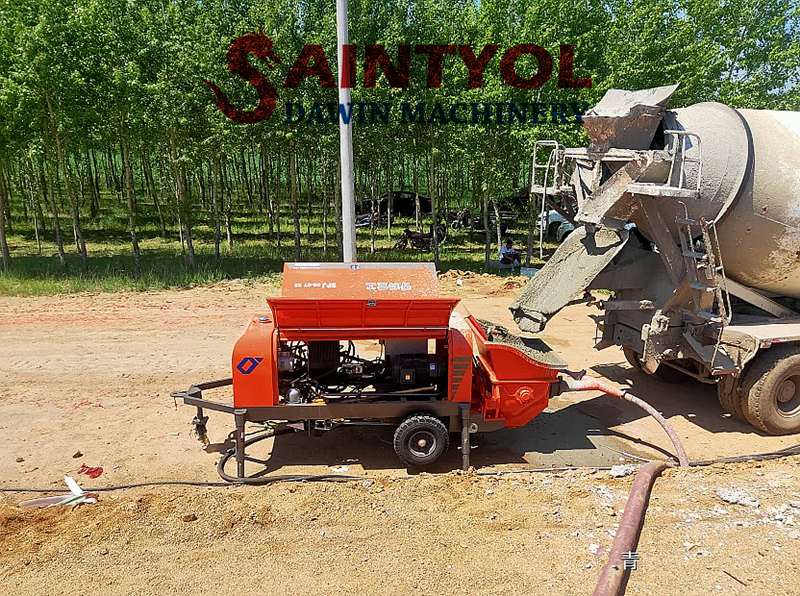
6. Control downtime
During shutdown, the pump should be turned on every 5 to 10 minutes (the specific time depends on the temperature of the day, the slump of concrete, and the initial setting time of concrete) to prevent pipe blockage. It is not advisable to continue pumping the concrete that has been set for too long after the downtime. When the concrete pumping process needs to be interrupted, the interruption time should not exceed 1 hour, and reverse pump and forward pump operation should be performed every 5 to 10 minutes to prevent the pipe from being blocked due to concrete bleeding or excessive slump loss .
7. Pay attention to temperature changes
In summer, the temperature is high, and the concrete is easy to dehydrate under the strong sunlight, which will lead to pipe blockage. Therefore, the pipe should be covered with wet grass and watered frequently. In winter, it should be wrapped with thermal insulation straw to avoid heat loss and affect the workability of concrete.
8. The method of emergency removal of blockage
(1) Repeat reverse pump and positive pump operation, gradually suck out the concrete and return it to the hopper, and then re-delivery after stirring
(2) Find out the clogged part by tapping with a hammer, etc. After the concrete is loosened, repeat the reverse pump and positive pump operation to eliminate the clog.
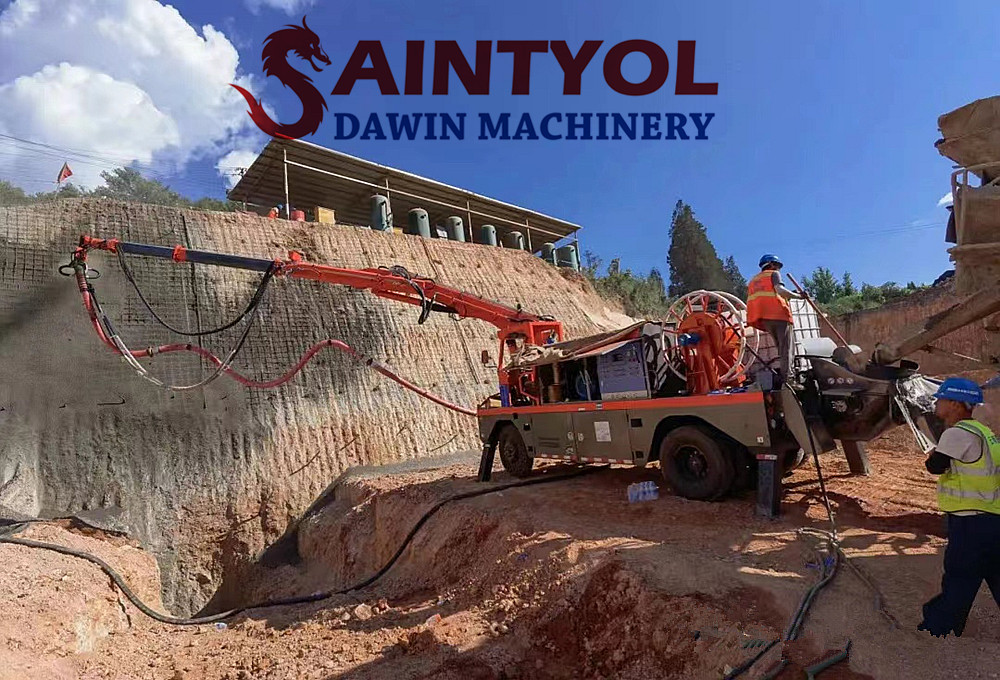